قالب ریختهگری ریژه | فرآیند، مزایا و کاربردها
ریختهگری ریژه چیست؟
ریختهگری ریژه یک روش ریختهگری ریژه است که در آن فلز مذاب به داخل قالب ریخته گری ریژه دائمی تزریق میشود. این روش ریختهگری ریژه به دلیل استفاده از قالبهای دائمی، مزایای ریختهگری ریژه نسبت به روشهای دیگر مانند ریختهگری ماسهای را دارد. در این روش، مذاب تحت فشار به داخل قالب تزریق میشود تا قطعاتی با تلرانس و دقت در ریختهگری ریژه بالا تولید شوند. از قالبگیری ریژه در ریختهگری معمولا برای تولید انبوه قطعات با کیفیت بالا استفاده میشود.


تعریف ریختهگری ریژه و تفاوت آن با سایر روشهای ریختهگری
ریختهگری ریژه یک روش ریختهگری ریژه پیشرفته است که در آن فلز مذاب به داخل قالب ریخته گری ریژه فلزی تزریق میشود. تفاوت اصلی این روش با سایر روشهای ریختهگری، استفاده از قالبگیری دائم در ریختهگری است. در حالی که در ریختهگری ماسهای از قالبهای یکبار مصرف استفاده میشود، در ریختهگری ریژه از قالبهای دائمی فلزی استفاده میشود که مزایای ریختهگری ریژه نسبت به روشهای دیگر را افزایش میدهد. این روش امکان تولید قطعات با تلرانس و دقت در ریختهگری ریژه بالاتر را فراهم میکند و نیاز به ماشینکاری بعد از ریختهگری ریژه را کاهش میدهد.
چرا از قالبهای دائمی در ریختهگری ریژه استفاده میشود؟
استفاده از قالبهای دائمی در قالبگیری ریژه در ریختهگری به دلیل مزایای ریختهگری ریژه نسبت به روشهای دیگر صورت میگیرد. قالب ریخته گری ریژه فلزی، امکان انتقال حرارت سریعتر را فراهم میکند که منجر به انجماد سریعتر و در نتیجه افزایش سختی و استحکام قطعات ریختهگری شده میشود. همچنین، استفاده از قالبگیری دائم در ریختهگری باعث افزایش تلرانس و دقت در ریختهگری ریژه و کاهش نیاز به ماشینکاری بعد از ریختهگری ریژه میشود. این عوامل باعث میشوند روش ریختهگری ریژه برای تولید انبوه قطعات با کیفیت بالا مناسب باشد.
فرآیند ریختهگری ریژه چگونه انجام میشود؟
فرآیند تولید قطعات فلزی با روش ریختهگری ریژه شامل چند مرحله اصلی است. ابتدا قالب ریخته گری ریژه که از مواد مناسب برای قالبهای ریژه ساخته شده، آماده میشود. سپس فلز مذاب به داخل قالب تزریق شده و تحت فشار قرار میگیرد تا تمام زوایای قالب پر شود. پس از انجماد فلز، قطعه از قالب خارج شده و در صورت نیاز عملیات حرارتی قطعات ریختهگری شده انجام میشود. این روش ریختهگری ریژه به دلیل استفاده از قالبگیری دائم در ریختهگری، امکان تولید قطعات با تلرانس و دقت در ریختهگری ریژه بالا را فراهم میکند.


مراحل طراحی و آمادهسازی قالب ریژه
طراحی قالب ریختهگری ریژه یک فرآیند حیاتی در قالبگیری ریژه در ریختهگری است. این مرحله شامل تعیین شکل و ابعاد دقیق قطعه، انتخاب مواد مناسب برای قالبهای ریژه و طراحی سیستمهای تغذیه و خنککننده است. در طراحی قالب ریختهگری ریژه باید به تلرانس و دقت در ریختهگری ریژه توجه ویژهای شود تا قطعات نهایی دارای ابعاد دقیق و کیفیت بالا باشند. پس از طراحی، قالب ساخته شده و قبل از استفاده، آزمایشهای لازم برای اطمینان از عملکرد صحیح آن انجام میشود. فرآیند تولید قطعات فلزی با روش ریختهگری ریژه به شدت وابسته به طراحی دقیق قالب است.


انتخاب مواد اولیه مناسب برای ریختهگری ریژه
انتخاب مواد مناسب برای قالبهای ریژه نقش مهمی در کیفیت قطعات تولیدی دارد. قالب ریخته گری ریژه باید از موادی ساخته شود که دارای استحکام بالا، مقاومت در برابر حرارت و سایش باشند. همچنین، آلیاژهای مناسب برای ریختهگری ریژه نیز باید با دقت انتخاب شوند. معمولاً از ریختهگری فلزات مانند آلومینیوم، روی و مس در این روش استفاده میشود. مواد مناسب برای قالبهای ریژه باید قابلیت تحمل دماهای بالا و فشارهای ناشی از تزریق مذاب را داشته باشند تا فرآیند تولید قطعات فلزی با روش ریختهگری ریژه به درستی انجام شود.
پر کردن قالب و خنکسازی قطعه
در روش ریختهگری ریژه، پر کردن قالب و خنکسازی قطعه دو مرحله حیاتی هستند. پس از آمادهسازی قالب ریخته گری ریژه، فلز مذاب با فشار به داخل قالب تزریق میشود تا تمام حفرهها و زوایای قالب پر شوند. سپس، قطعه باید به طور یکنواخت خنک شود تا از ایجاد ترک و تنشهای داخلی جلوگیری شود. سرعت خنکسازی تأثیر زیادی بر سختی و استحکام قطعات ریختهگری شده دارد. فرآیند تولید قطعات فلزی با روش ریختهگری ریژه نیازمند کنترل دقیق دما و فشار در این مراحل است.
مواد مورد استفاده در ریختهگری ریژه
در ریختهگری فلزات به روش ریژه، از مواد مختلفی برای ساخت قالب ریخته گری ریژه و تولید قطعات استفاده میشود. برای ساخت قالبها معمولاً از فولادهای آلیاژی با مقاومت بالا در برابر حرارت و سایش استفاده میشود. آلیاژهای مناسب برای ریختهگری ریژه شامل آلومینیوم، روی، مس و آلیاژهای آنها هستند. انتخاب مواد مناسب بستگی به طراحی قالب ریختهگری ریژه و خواص مورد نیاز قطعه نهایی دارد. استفاده از مواد مناسب برای قالبهای ریژه باعث افزایش تلرانس و دقت در ریختهگری ریژه میشود.


آلیاژهای آلومینیوم و کاربرد آن در قالبگیری ریژه
آلیاژهای آلومینیوم به دلیل وزن سبک، مقاومت بالا در برابر خوردگی و قابلیت ریختهگری فلزات، به طور گسترده در قالبگیری ریژه در ریختهگری استفاده میشوند. آلیاژهای مناسب برای ریختهگری ریژه آلومینیوم شامل آلیاژهای سری A380، A356 و A413 هستند که هر کدام خواص مکانیکی و حرارتی متفاوتی دارند. قالبگیری ریژه در ریختهگری با استفاده از آلیاژهای آلومینیوم، امکان تولید قطعات پیچیده با تلرانس و دقت در ریختهگری ریژه بالا را فراهم میکند. این آلیاژها به دلیل مزایای ریختهگری ریژه نسبت به روشهای دیگر، در صنایع مختلف کاربرد دارند.
ریختهگری قطعات فولادی با روش ریژه
ریختهگری فلزات فولادی با روش ریختهگری ریژه چالشهای خاص خود را دارد، اما با استفاده از تکنولوژیهای پیشرفته و مواد مناسب برای قالبهای ریژه، امکانپذیر است. برای ریختهگری فلزات فولادی، قالبها باید از موادی ساخته شوند که مقاومت بالایی در برابر حرارت و فشار داشته باشند. همچنین، فرآیند تولید قطعات فلزی با روش ریختهگری ریژه باید به گونهای کنترل شود که از ایجاد ترک و عیوب دیگر در قطعه جلوگیری شود. با وجود این چالشها، مزایای ریختهگری ریژه نسبت به روشهای دیگر مانند دقت بالا و سطح صاف، باعث شده است که این روش برای تولید قطعات فولادی خاص مورد توجه قرار گیرد.
تأثیر عملیات حرارتی بر قطعات ریختهگری شده
عملیات حرارتی قطعات ریختهگری شده نقش مهمی در بهبود خواص مکانیکی و فیزیکی آنها دارد. این فرآیند شامل گرم کردن قطعات تا دمای مشخص و سپس خنک کردن آنها با سرعت معین است. عملیات حرارتی قطعات ریختهگری شده میتواند سختی و استحکام قطعات ریختهگری شده را افزایش دهد، تنشهای داخلی را کاهش دهد و خواص ماشینکاری آنها را بهبود بخشد. انتخاب نوع عملیات حرارتی قطعات ریختهگری شده بستگی به نوع آلیاژ و خواص مورد نیاز قطعه دارد. این فرآیند به عنوان یک مرحله تکمیلی در فرآیند تولید قطعات فلزی با روش ریختهگری ریژه انجام میشود.
مزایای استفاده از قالبهای ریژه در ریختهگری
مزایای استفاده از قالبهای فلزی در ریختهگری ریژه بسیار زیاد است. قالب ریخته گری ریژه دائمی است و میتواند برای تولید تعداد زیادی قطعه استفاده شود. این امر منجر به کاهش هزینههای تولید و افزایش سرعت تولید میشود. همچنین، قالب ریخته گری ریژه امکان تولید قطعات با تلرانس و دقت در ریختهگری ریژه بالا را فراهم میکند و نیاز به ماشینکاری بعد از ریختهگری ریژه را کاهش میدهد. مزایای استفاده از قالبهای فلزی در ریختهگری باعث شده است که این روش به یکی از پرکاربردترین روشهای ریختهگری تبدیل شود.


دقت ابعادی بالا و کاهش نیاز به ماشینکاری
یکی از مهمترین مزایای ریختهگری ریژه نسبت به روشهای دیگر، دقت ابعادی بالای قطعات تولیدی است. استفاده از قالب ریخته گری ریژه دائمی و کنترل دقیق فرآیند تولید قطعات فلزی با روش ریختهگری ریژه، امکان تولید قطعات با تلرانس و دقت در ریختهگری ریژه بسیار بالا را فراهم میکند. این امر باعث کاهش نیاز به ماشینکاری بعد از ریختهگری ریژه میشود و در نتیجه هزینههای تولید کاهش مییابد. مزایای ریختهگری ریژه نسبت به روشهای دیگر در این زمینه، باعث شده است که این روش برای تولید قطعات پیچیده و دقیق بسیار مناسب باشد.
افزایش سرعت تولید قطعات صنعتی
مزایای ریختهگری ریژه نسبت به روشهای دیگر شامل افزایش سرعت تولید قطعات صنعتی است. استفاده از قالبگیری دائم در ریختهگری و دستگاههای مورد استفاده در ریختهگری ریژه مدرن، امکان تولید تعداد زیادی قطعه در زمان کوتاه را فراهم میکند. فرآیند تولید قطعات فلزی با روش ریختهگری ریژه به صورت خودکار و پیوسته انجام میشود که باعث افزایش سرعت تولید میشود. این مزایای ریختهگری ریژه نسبت به روشهای دیگر باعث شده است که این روش برای تولید انبوه قطعات صنعتی بسیار مقرون به صرفه باشد.
استحکام و مقاومت بالای قطعات ریختهگری شده
سختی و استحکام قطعات ریختهگری شده با روش ریژه به دلیل مزایای ریختهگری ریژه نسبت به روشهای دیگر بسیار بالا است. فرآیند تولید قطعات فلزی با روش ریختهگری ریژه باعث میشود که قطعات دارای ساختار متراکم و بدون حباب باشند. همچنین، استفاده از مواد مناسب برای قالبهای ریژه و عملیات حرارتی قطعات ریختهگری شده میتواند سختی و استحکام قطعات ریختهگری شده را بهبود بخشد. این مزایای ریختهگری ریژه نسبت به روشهای دیگر باعث شده است که قطعات تولید شده با این روش در برابر فشار، ضربه و سایش مقاومت بالایی داشته باشند.
معایب و محدودیتهای ریختهگری ریژه
با وجود مزایای ریختهگری ریژه نسبت به روشهای دیگر، این روش دارای معایب و محدودیتهایی نیز است. یکی از معایب اصلی، هزینه بالای طراحی قالب ریختهگری ریژه و ساخت قالب ریخته گری ریژه است. همچنین، روش ریختهگری ریژه برای تولید قطعات با ابعاد بزرگ و پیچیدگیهای زیاد محدودیت دارد. علاوه بر این، مواد مناسب برای قالبهای ریژه باید دارای خواص خاصی باشند که این امر انتخاب مواد را محدود میکند. با این حال، با توجه به مزایای ریختهگری ریژه نسبت به روشهای دیگر، این روش همچنان برای تولید بسیاری از قطعات صنعتی مورد استفاده قرار میگیرد.
هزینه بالای تولید قالبهای فلزی ریژه
هزینه بالای تولید قالب ریخته گری ریژه یکی از معایب اصلی این روش است. طراحی قالب ریختهگری ریژه نیازمند تخصص و دقت بالایی است و ساخت قالبها نیز نیازمند دستگاههای مورد استفاده در ریختهگری ریژه پیشرفته و مواد با کیفیت است. مواد مناسب برای قالبهای ریژه معمولاً گرانقیمت هستند و فرآیند ساخت قالبها نیز زمانبر است. این عوامل باعث میشوند که هزینه تولید قالب ریخته گری ریژه بسیار بالا باشد. با این حال، با توجه به مزایای ریختهگری ریژه نسبت به روشهای دیگر، این هزینه در تولید انبوه قطعات جبران میشود.
محدودیت در طراحی و تغییرات قالبها
یکی از محدودیتهای روش ریختهگری ریژه، محدودیت در طراحی قالب ریختهگری ریژه و تغییرات قالبها است. قالب ریخته گری ریژه پس از ساخت، به سختی قابل تغییر است و ایجاد تغییرات در طراحی قالب ریختهگری ریژه نیازمند هزینه و زمان زیادی است. این محدودیت باعث میشود که روش ریختهگری ریژه برای تولید قطعات با طراحیهای پیچیده و تغییرات زیاد مناسب نباشد. با این حال، با استفاده از تکنولوژیهای پیشرفته در طراحی قالب ریختهگری ریژه، میتوان این محدودیت را تا حدی کاهش داد.
کاربردهای ریختهگری ریژه در صنایع مختلف
روش ریختهگری ریژه به دلیل مزایای ریختهگری ریژه نسبت به روشهای دیگر در صنایع مختلف کاربرد دارد. از جمله کاربردهای این روش میتوان به تولید قطعات خودرو، قطعات هوافضا، قطعات الکتریکی و قطعات صنعتی اشاره کرد. قالبگیری ریژه در ریختهگری امکان تولید قطعات با تلرانس و دقت در ریختهگری ریژه بالا را فراهم میکند که برای بسیاری از کاربردها ضروری است. استفاده از روش ریختهگری ریژه در صنایع مختلف به دلیل افزایش سرعت تولید، کاهش هزینهها و بهبود کیفیت قطعات، روز به روز در حال افزایش است.


استفاده از ریختهگری ریژه در خودروسازی
در صنعت خودروسازی، ریختهگری فلزات به روش ریختهگری ریژه به طور گسترده برای تولید قطعات مختلف مورد استفاده قرار میگیرد. قطعاتی مانند بلوک سیلندر، سرسیلندر، پیستون و چرخها با استفاده از قالبگیری ریژه در ریختهگری تولید میشوند. مزایای ریختهگری ریژه نسبت به روشهای دیگر در این صنعت شامل دقت بالا، سطح صاف و سختی و استحکام قطعات ریختهگری شده است. استفاده از روش ریختهگری ریژه در خودروسازی باعث کاهش وزن قطعات، افزایش عمر مفید آنها و بهبود عملکرد خودرو میشود.
کاربرد این روش در تولید قطعات هوافضا
در صنعت هوافضا، ریختهگری فلزات با استفاده از روش ریختهگری ریژه برای تولید قطعاتی که نیاز به تلرانس و دقت در ریختهگری ریژه بالا دارند، استفاده میشود. قطعاتی مانند پرههای توربین، قطعات موتور و قطعات سازهای با استفاده از قالبگیری ریژه در ریختهگری تولید میشوند. مزایای ریختهگری ریژه نسبت به روشهای دیگر در این صنعت شامل مقاومت بالا در برابر حرارت و فشار، وزن سبک و دقت ابعادی است. استفاده از روش ریختهگری ریژه در هوافضا باعث افزایش ایمنی و بهبود عملکرد هواپیماها میشود.
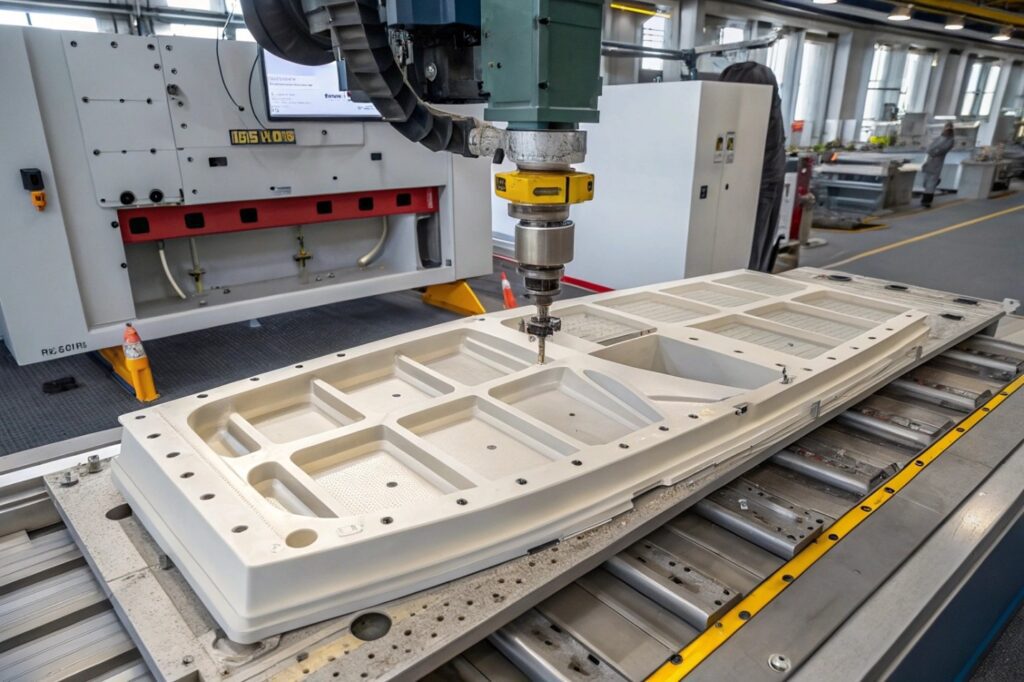
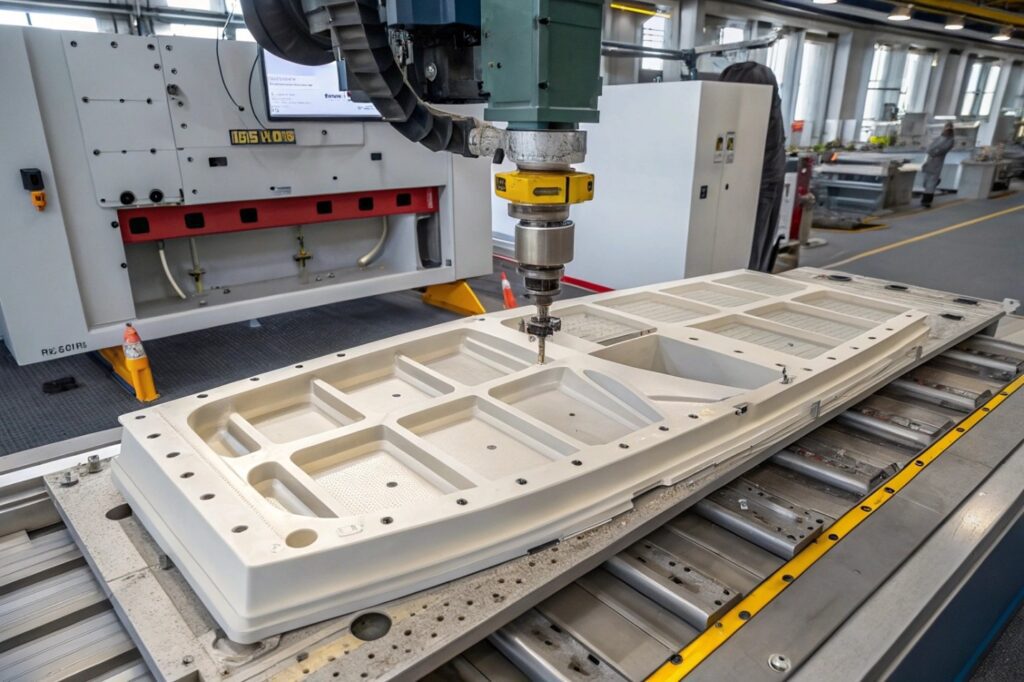
ریختهگری قطعات صنعتی و تجهیزات الکتریکی
روش ریختهگری ریژه در تولید قطعات صنعتی و تجهیزات الکتریکی کاربردهای فراوانی دارد. قطعاتی مانند بدنه موتورها، جعبه دندهها، قطعات پمپ و قطعات الکترونیکی با استفاده از قالبگیری ریژه در ریختهگری تولید میشوند. مزایای ریختهگری ریژه نسبت به روشهای دیگر در این صنایع شامل دقت بالا، سطح صاف و سختی و استحکام قطعات ریختهگری شده است. استفاده از روش ریختهگری ریژه در تولید قطعات صنعتی و تجهیزات الکتریکی باعث افزایش عمر مفید آنها و بهبود عملکرد دستگاهها میشود.
جمعبندی
روش ریختهگری ریژه یک فرآیند مهم در ریختهگری فلزات است که از قالب ریخته گری ریژه دائمی برای تولید قطعات با تلرانس و دقت در ریختهگری ریژه بالا استفاده میکند. مزایای ریختهگری ریژه نسبت به روشهای دیگر شامل سرعت تولید بالا، کاهش نیاز به ماشینکاری بعد از ریختهگری ریژه و سختی و استحکام قطعات ریختهگری شده است. با وجود هزینه بالای طراحی قالب ریختهگری ریژه و محدودیت در تغییرات قالب، این روش در صنایع مختلف مانند خودروسازی، هوافضا و تولید قطعات صنعتی کاربرد گستردهای دارد. استفاده از مواد مناسب برای قالبهای ریژه و عملیات حرارتی قطعات ریختهگری شده میتواند کیفیت قطعات تولیدی را بهبود بخشد.
سوالات متداول درباره ریختهگری ریژه
تفاوت ریختهگری ریژه و ریختهگری ماسهای چیست؟
مقایسه ریختهگری ریژه و ریختهگری ماسهای نشان میدهد که تفاوت اصلی در نوع قالب مورد استفاده است. در ریختهگری ریژه از قالب ریخته گری ریژه دائمی استفاده میشود، در حالی که در ریختهگری ماسهای از قالبهای یکبار مصرف ماسهای استفاده میشود. مزایای ریختهگری ریژه نسبت به روشهای دیگر شامل دقت بالاتر، سطح صافتر و سرعت تولید بیشتر است. مقایسه ریختهگری ریژه و ریختهگری ماسهای نشان میدهد که ریختهگری ریژه برای تولید انبوه قطعات با کیفیت بالا مناسبتر است.
چه موادی برای قالبگیری ریژه مناسبتر هستند؟
مواد مناسب برای قالبهای ریژه باید دارای خواص خاصی باشند. این مواد باید مقاومت بالایی در برابر حرارت و سایش داشته باشند و همچنین قابلیت انتقال حرارت خوبی داشته باشند. معمولاً از فولادهای آلیاژی، چدن خاکستری و آلیاژهای مس برای ساخت قالب ریخته گری ریژه استفاده میشود. انتخاب مواد مناسب برای قالبهای ریژه بستگی به نوع ریختهگری فلزات و دمای مذاب دارد. استفاده از مواد مناسب برای قالبهای ریژه باعث افزایش عمر مفید قالب و بهبود کیفیت قطعات تولیدی میشود.
مزایای استفاده از ریختهگری ریژه در خودروسازی چیست؟
مزایای ریختهگری ریژه نسبت به روشهای دیگر در صنعت خودروسازی بسیار زیاد است. قالبگیری ریژه در ریختهگری امکان تولید قطعات با دقت بالا و سطح صاف را فراهم میکند که نیاز به ماشینکاری بعد از ریختهگری ریژه را کاهش میدهد. همچنین، روش ریختهگری ریژه باعث افزایش سرعت تولید و کاهش هزینهها میشود. مزایای ریختهگری ریژه نسبت به روشهای دیگر در خودروسازی شامل کاهش وزن قطعات، افزایش عمر مفید آنها و بهبود عملکرد خودرو است.
آیا امکان تولید قطعات پیچیده با قالب ریژه وجود دارد؟
با استفاده از طراحی قالب ریختهگری ریژه مناسب و دستگاههای مورد استفاده در ریختهگری ریژه پیشرفته، امکان تولید قطعات پیچیده با قالب ریخته گری ریژه وجود دارد. طراحی قالب ریختهگری ریژه باید به گونهای باشد که تمام زوایای قالب به درستی پر شوند و هیچ حبابی در قطعه ایجاد نشود. استفاده از سیستمهای تغذیه و خنککننده مناسب نیز در تولید قطعات پیچیده با روش ریختهگری ریژه ضروری است.
هزینه تولید قالبهای ریژه چگونه محاسبه میشود؟
هزینه تولید قالب ریخته گری ریژه بستگی به عوامل مختلفی دارد. طراحی قالب ریختهگری ریژه، مواد مناسب برای قالبهای ریژه، دستگاههای مورد استفاده در ریختهگری ریژه و زمان تولید قالب از جمله عوامل موثر در هزینه تولید هستند. طراحی قالب ریختهگری ریژه پیچیدهتر و استفاده از مواد مناسب برای قالبهای ریژه گرانقیمتتر، هزینه تولید قالب را افزایش میدهند. همچنین، استفاده از دستگاههای مورد استفاده در ریختهگری ریژه پیشرفته و فرآیندهای پیچیده تولید نیز هزینه را افزایش میدهند.