طراحی قالبهای باکالیت | فرآیند، استانداردها و ویژگیهای مواد
قالبهای باکالیت، ابزاری حیاتی در شکلدهی مواد باکالیتی هستند. طراحی قالب های باکالیت به گونهای انجام میشود که امکان تولید قطعات با اشکال پیچیده را فراهم کند. مواد اولیه در قالبهای باکالیت معمولاً رزین فنولیک است که پس از پخت، خواص مکانیکی و حرارتی بسیار خوبی از خود نشان میدهد. فرآیند قالبگیری باکالیت معمولاً شامل فشردهسازی یا تزریق مواد به داخل قالب است. از قالبهای باکالیت در تولید قطعات متنوعی مانند دستگیرههای عایق، قطعات الکتریکی و تزئینات استفاده میشود. انتخاب مواد اولیه در قالبهای باکالیت باید با دقت صورت گیرد تا محصول نهایی از کیفیت بالایی برخوردار باشد.


ویژگیهای فیزیکی و شیمیایی باکالیت
باکالیت به عنوان یک رزین ترموست، ویژگیهای منحصر به فردی دارد. ویژگیهای حرارتی و مکانیکی باکالیت شامل مقاومت بالا در برابر حرارت، استحکام مکانیکی خوب و عایق الکتریکی بودن است. فرآیند قالبگیری باکالیت به دلیل این ویژگیها، برای تولید قطعاتی که در شرایط سخت کاری قرار دارند، مناسب است. مواد اولیه در قالبهای باکالیت، پس از پخت، ساختاری سخت و غیرقابل انعطاف پیدا میکنند. تحلیل استحکام و دوام قطعات باکالیتی نشان میدهد که این مواد میتوانند در برابر خوردگی و مواد شیمیایی مقاومت خوبی داشته باشند. رزین فنولیک و کاربرد آن در قالبگیری باکالیت، نقش کلیدی در تعیین این ویژگیها دارد.
مزایا و معایب استفاده از قالبهای باکالیت
استفاده از قالبهای باکالیت مزایای متعددی دارد. یکی از مهمترین مزایا، مقاومت حرارتی بالای قطعات تولید شده است. فرآیند قالبگیری باکالیت به دلیل استفاده از رزین فنولیک، قطعاتی با استحکام و دوام بالا تولید میکند. با این حال، محدودیتهای طراحی قالبهای باکالیت نیز وجود دارد؛ به عنوان مثال، طراحی قالب های باکالیت باید به گونهای باشد که از ایجاد ترک و تابیدگی در قطعات جلوگیری شود. از معایب دیگر میتوان به زمان طولانیتر فرآیند پخت در مقایسه با ترموپلاستیکها اشاره کرد. مواد اولیه در قالبهای باکالیت نیز میتواند گرانتر از برخی مواد دیگر باشد.
فرآیند طراحی و ساخت قالبهای باکالیت
فرآیند طراحی قالب های باکالیت شامل مراحل مختلفی است. ابتدا نیاز است تحلیل جریان مواد در قالبهای باکالیت انجام شود تا از پر شدن کامل حفرهها اطمینان حاصل شود. استانداردهای طراحی قالبهای باکالیت باید رعایت شوند تا قالب بتواند در تولید انبوه عملکرد مناسبی داشته باشد. انتخاب بهترین متریال برای تولید قطعات باکالیتی نیز در این مرحله اهمیت دارد. سیستمهای راهگاهی و خنککننده در قالبهای باکالیت باید به دقت طراحی شوند تا از ایجاد عیوب جلوگیری شود. طراحی قالب های باکالیت با استفاده از نرمافزارهای CAD/CAM انجام میشود.


مراحل طراحی قالبهای باکالیت
مراحل طراحی قالب های باکالیت شامل تعیین ابعاد قطعه، طراحی سیستمهای راهگاهی و خنککننده و انتخاب مواد مناسب برای قالب است. تحلیل جریان مواد در قالبهای باکالیت به کمک نرمافزارهای شبیهسازی انجام میشود تا مشکلات احتمالی شناسایی شوند. استانداردهای طراحی قالبهای باکالیت باید در تمام مراحل رعایت شوند تا قالب دارای استحکام و دقت کافی باشد. سیستمهای راهگاهی و خنککننده در قالبهای باکالیت باید به گونهای طراحی شوند که دما و فشار به طور یکنواخت توزیع شوند. محدودیتهای طراحی قالبهای باکالیت نیز باید در نظر گرفته شوند تا از بروز مشکلاتی مانند تابیدگی و ترکخوردگی جلوگیری شود.
استانداردهای طراحی قالب برای تولید انبوه
رعایت استانداردهای طراحی قالبهای باکالیت برای تولید انبوه، امری ضروری است. این استانداردها شامل مواردی مانند انتخاب مواد مناسب برای قالب، طراحی سیستمهای خنککننده و راهگاهی و تعیین ابعاد دقیق قالب است. روشهای بهینهسازی قالب برای تولید انبوه باید به گونهای باشند که زمان تولید کاهش یابد و کیفیت قطعات تولیدی افزایش یابد. تحلیل جریان مواد در قالبهای باکالیت به کمک نرمافزارهای شبیهسازی به شناسایی و رفع مشکلات احتمالی کمک میکند. طراحی قالب های باکالیت باید به گونهای باشد که امکان تعویض آسان قطعات فرسوده وجود داشته باشد. استانداردهای طراحی قالبهای باکالیت به افزایش عمر مفید قالب کمک میکند.
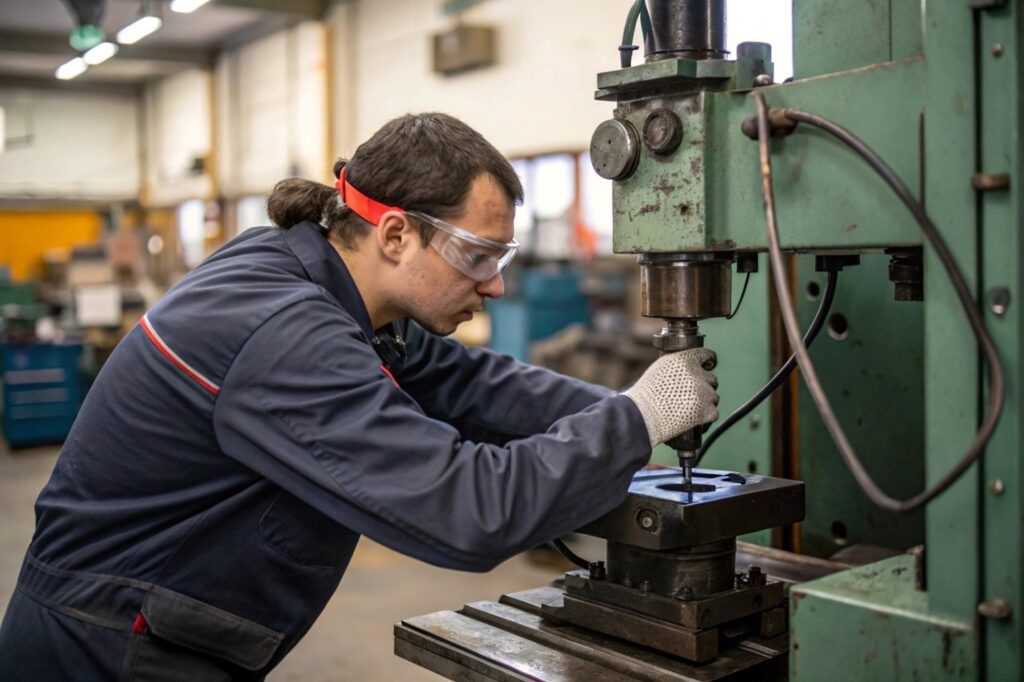
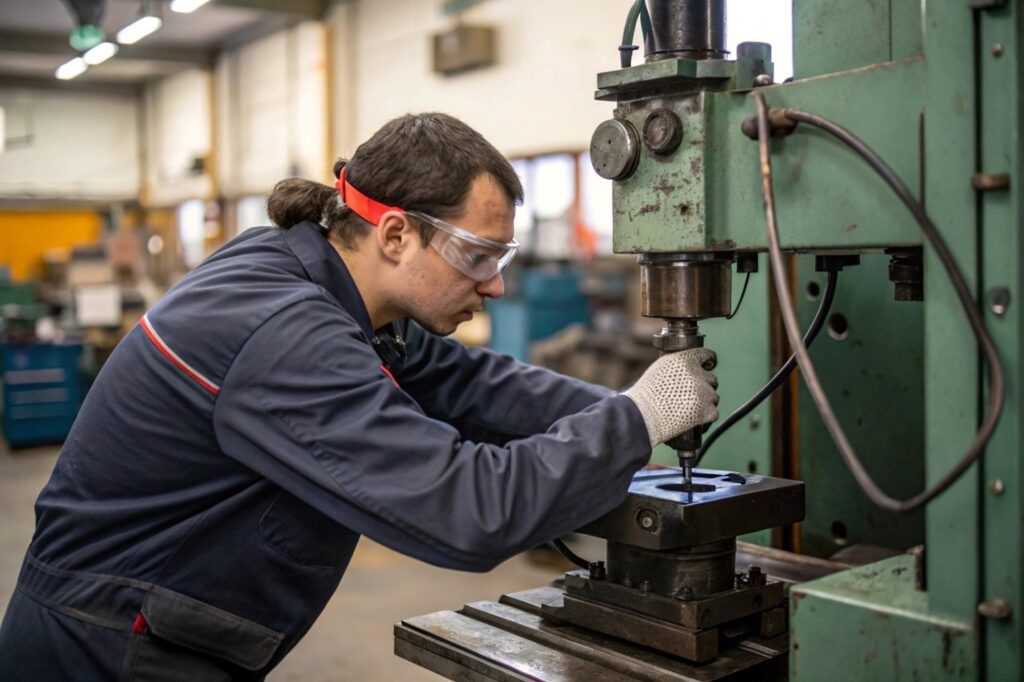
انتخاب بهترین متریال برای قالبگیری باکالیت
انتخاب بهترین متریال برای تولید قطعات باکالیتی، تأثیر زیادی بر کیفیت و دوام محصول نهایی دارد. مواد اولیه در قالبهای باکالیت باید دارای مقاومت حرارتی و مکانیکی مناسب باشند. ویژگیهای حرارتی و مکانیکی باکالیت، انتخاب مواد قالب را تحت تأثیر قرار میدهد. استانداردهای طراحی قالبهای باکالیت نیز مشخصات مواد مورد استفاده را تعیین میکنند. فرآیند قالبگیری باکالیت نیاز به موادی دارد که در برابر فشار و حرارت بالا مقاوم باشند. تحلیل استحکام و دوام قطعات باکالیتی نشان میدهد که استفاده از مواد با کیفیت، عمر مفید قطعات را افزایش میدهد. رزین فنولیک و کاربرد آن در قالبگیری باکالیت نیز نقش مهمی در این انتخاب دارد.
روشهای قالبگیری باکالیت
فرآیند قالبگیری باکالیت شامل روشهای مختلفی است که هر کدام مزایا و معایب خاص خود را دارند. فرآیند فشردهسازی در قالبگیری باکالیت یکی از روشهای رایج است که در آن مواد اولیه تحت فشار و حرارت قرار میگیرند. روشهای بهینهسازی قالب برای تولید انبوه نیز بر اساس نوع فرآیند قالبگیری انتخاب میشوند. ماشینهای قالبگیری باکالیت و تنظیمات آنها نیز بسته به روش قالبگیری متفاوت است. تأثیر فشار و دما بر کیفیت قالبگیری باکالیت در هر روش متفاوت است و باید به دقت کنترل شود. مواد اولیه در قالبهای باکالیت نیز بسته به روش قالبگیری انتخاب میشوند.


فرآیند فشردهسازی در قالبگیری باکالیت
فرآیند فشردهسازی در قالبگیری باکالیت، یکی از روشهای اصلی تولید قطعات باکالیتی است. در این روش، مواد اولیه در قالبهای باکالیت تحت فشار و حرارت قرار میگیرند تا شکل مورد نظر را به خود بگیرند. تأثیر فشار و دما بر کیفیت قالبگیری باکالیت در این روش بسیار مهم است. فرآیند فشردهسازی در قالبگیری باکالیت نیاز به ماشینهای قالبگیری باکالیت و تنظیمات دقیق دارد. مواد اولیه در قالبهای باکالیت باید به گونهای انتخاب شوند که در برابر فشار و حرارت بالا مقاوم باشند. تحلیل جریان مواد در قالبهای باکالیت در این روش به بهینهسازی فرآیند کمک میکند.
فرآیند تزریق و فشار بالا در قالبگیری باکالیت
فرآیند تزریق و فشار بالا در قالبگیری باکالیت، یکی از روشهای پیشرفته تولید قطعات باکالیتی است. در این روش، مواد اولیه در قالبهای باکالیت تحت فشار بسیار بالا به داخل قالب تزریق میشوند. تأثیر فشار و دما بر کیفیت قالبگیری باکالیت در این روش بسیار مهم است و باید به دقت کنترل شود. ماشینهای قالبگیری باکالیت و تنظیمات آنها در این روش نقش حیاتی دارند. تحلیل جریان مواد در قالبهای باکالیت به کمک نرمافزارهای شبیهسازی به بهینهسازی فرآیند تزریق کمک میکند. این روش معمولاً برای تولید قطعات پیچیده و با دقت بالا استفاده میشود.
عیوب رایج در قالبگیری باکالیت و روشهای رفع آن
عیوب رایج در قالبگیری باکالیت و روشهای رفع آن، یکی از دغدغههای اصلی تولیدکنندگان است. ترکخوردگی، تابیدگی، و عدم پر شدن کامل قالب از جمله این عیوب هستند. عیوب رایج در قالبگیری باکالیت و روشهای رفع آن شامل تنظیم دقیق دما و فشار، بهینهسازی سیستمهای راهگاهی و خنککننده و انتخاب مواد اولیه مناسب است. تحلیل جریان مواد در قالبهای باکالیت به شناسایی و رفع این عیوب کمک میکند. استانداردهای طراحی قالبهای باکالیت نیز در کاهش این عیوب مؤثر است. روشهای بهینهسازی قالب برای تولید انبوه نیز باید به گونهای باشند که از بروز این عیوب جلوگیری کنند.


ترکخوردگی و تغییر شکل در قطعات باکالیتی
ترکخوردگی و تغییر شکل در قطعات باکالیتی میتواند ناشی از عوامل مختلفی باشد. تنشهای داخلی، دمای نامناسب و فشار بیش از حد در فرآیند قالبگیری میتوانند به این مشکلات منجر شوند. فرآیند قالبگیری باکالیت باید به گونهای کنترل شود که از ایجاد این تنشها جلوگیری شود. استانداردهای طراحی قالبهای باکالیت نیز در کاهش این مشکلات مؤثر است. تحلیل جریان مواد در قالبهای باکالیت به شناسایی نقاط ضعف و بهینهسازی فرآیند کمک میکند. انتخاب بهترین متریال برای تولید قطعات باکالیتی نیز در کاهش ترکخوردگی و تغییر شکل مؤثر است.
روشهای بهینهسازی کیفیت محصول نهایی
روشهای بهینهسازی قالب برای تولید انبوه با کیفیت بالا، شامل کنترل دقیق دما و فشار، بهینهسازی سیستمهای راهگاهی و خنککننده و استفاده از مواد اولیه با کیفیت است. ویژگیهای حرارتی و مکانیکی باکالیت نیز باید در نظر گرفته شوند. تأثیر فشار و دما بر کیفیت قالبگیری باکالیت بسیار زیاد است و باید به دقت کنترل شود. تحلیل جریان مواد در قالبهای باکالیت به شناسایی و رفع مشکلات احتمالی کمک میکند. روشهای خنککاری در قالبگیری باکالیت نیز نقش مهمی در کیفیت محصول نهایی دارد.
تأثیر دما و فشار بر فرآیند قالبگیری باکالیت
تأثیر فشار و دما بر کیفیت قالبگیری باکالیت بسیار زیاد است. دمای بالا باعث تسریع فرآیند پخت میشود، اما اگر دما بیش از حد باشد، میتواند منجر به سوختن مواد و کاهش کیفیت قطعه شود. فشار مناسب نیز باعث پر شدن کامل قالب و افزایش استحکام قطعه میشود. ویژگیهای حرارتی و مکانیکی باکالیت باید در تنظیم دما و فشار در نظر گرفته شوند. ماشینهای قالبگیری باکالیت و تنظیمات آنها باید به گونهای باشند که دما و فشار به طور دقیق کنترل شوند. تحلیل جریان مواد در قالبهای باکالیت به تعیین بهترین دما و فشار برای هر قطعه کمک میکند.


تنظیم دما برای جلوگیری از نقص در قطعات
تنظیم دقیق دما در فرآیند قالبگیری باکالیت برای جلوگیری از نقص در قطعات بسیار مهم است. دمای نامناسب میتواند منجر به ترکخوردگی، تابیدگی و عدم پر شدن کامل قالب شود. ویژگیهای حرارتی و مکانیکی باکالیت باید در تنظیم دما در نظر گرفته شوند. روشهای خنککاری در قالبگیری باکالیت نیز نقش مهمی در کنترل دما دارند. ماشینهای قالبگیری باکالیت و تنظیمات آنها باید به گونهای باشند که دما به طور دقیق کنترل شود. تحلیل جریان مواد در قالبهای باکالیت به تعیین بهترین دما برای هر قطعه کمک میکند.
تأثیر فشار قالبگیری بر استحکام و دوام قطعات
تأثیر فشار و دما بر کیفیت قالبگیری باکالیت و به ویژه بر استحکام و دوام قطعات بسیار مهم است. فشار مناسب باعث پر شدن کامل قالب و ایجاد پیوند قوی بین مولکولهای مواد میشود. فرآیند فشردهسازی در قالبگیری باکالیت باید به گونهای انجام شود که فشار به طور یکنواخت توزیع شود. تحلیل استحکام و دوام قطعات باکالیتی نشان میدهد که قطعاتی که تحت فشار مناسب تولید شدهاند، عمر مفید بیشتری دارند. ماشینهای قالبگیری باکالیت و تنظیمات آنها باید به گونهای باشند که فشار به طور دقیق کنترل شود.
مقایسه قالبگیری باکالیت و سایر پلیمرها
مقایسه قالبگیری باکالیت و ترموپلاستیکها نشان میدهد که هر کدام مزایا و معایب خاص خود را دارند. فرآیند قالبگیری باکالیت معمولاً نیاز به زمان پخت بیشتری دارد، اما قطعات تولید شده دارای مقاومت حرارتی بالاتری هستند. مواد اولیه در قالبهای باکالیت نیز متفاوت از ترموپلاستیکها است. تحلیل جریان مواد در قالبهای باکالیت و ترموپلاستیکها نیز متفاوت است. روشهای خنککاری در قالبگیری باکالیت نیز با ترموپلاستیکها تفاوت دارد. انتخاب بین باکالیت و ترموپلاستیکها بستگی به کاربرد نهایی قطعه دارد.


تفاوت بین ترموست و ترموپلاستیکها در قالبگیری
تفاوت بین ترموست و ترموپلاستیکها در قالبگیری بسیار مهم است. مواد ترموست پس از پخت، ساختاری سخت و غیرقابل انعطاف پیدا میکنند، در حالی که ترموپلاستیکها را میتوان چندین بار ذوب و دوباره شکل داد. ویژگیهای حرارتی و مکانیکی باکالیت به عنوان یک ترموست، با ترموپلاستیکها متفاوت است. فرآیند قالبگیری باکالیت نیاز به دما و فشار بالاتری نسبت به ترموپلاستیکها دارد. محدودیتهای طراحی قالبهای باکالیت نیز با ترموپلاستیکها تفاوت دارد. مواد اولیه در قالبهای باکالیت نیز با ترموپلاستیکها متفاوت است.
چرا باکالیت برای کاربردهای صنعتی ترجیح داده میشود؟
باکالیت به دلیل ویژگیهای منحصر به فرد خود، برای کاربردهای صنعتی ترجیح داده میشود. مقاومت حرارتی بالا، استحکام مکانیکی خوب و عایق الکتریکی بودن از جمله این ویژگیها هستند. ویژگیهای حرارتی و مکانیکی باکالیت آن را برای استفاده در شرایط سخت کاری مناسب میسازد. فرآیند قالبگیری باکالیت به دلیل استفاده از رزین فنولیک، قطعاتی با دوام بالا تولید میکند. محدودیتهای طراحی قالبهای باکالیت در مقایسه با مزایای آن، قابل چشمپوشی است. مواد اولیه در قالبهای باکالیت نیز به گونهای انتخاب میشوند که این ویژگیها را تقویت کنند.
جمعبندی
در این بررسی، به جنبههای مختلف طراحی قالب های باکالیت، فرآیند قالبگیری باکالیت، و ویژگیهای مواد باکالیتی پرداخته شد. از انتخاب مواد اولیه در قالبهای باکالیت تا روشهای خنککاری در قالبگیری باکالیت، هر مرحله از فرآیند تولید اهمیت دارد. استانداردهای طراحی قالبهای باکالیت باید رعایت شوند تا قطعات با کیفیت و دوام بالا تولید شوند. تحلیل جریان مواد در قالبهای باکالیت به بهینهسازی فرآیند کمک میکند. ماشینهای قالبگیری باکالیت و تنظیمات آنها نیز نقش مهمی در کیفیت محصول نهایی دارند.
سوالات متداول درباره طراحی قالبهای باکالیت
در این بخش به برخی از سوالات متداول درباره طراحی قالب های باکالیت پاسخ داده میشود. این سوالات شامل مواردی مانند انتخاب بهترین متریال برای تولید قطعات باکالیتی، روشهای بهینهسازی قالب برای تولید انبوه و عیوب رایج در قالبگیری باکالیت و روشهای رفع آن است. استانداردهای طراحی قالبهای باکالیت نیز یکی از موضوعات مورد بحث است. فرآیند قالبگیری باکالیت و مراحل آن نیز مورد بررسی قرار میگیرد. این سوالات و پاسخها به درک بهتر فرآیند طراحی قالب های باکالیت کمک میکند.
چرا از باکالیت در تولید قطعات صنعتی استفاده میشود؟
باکالیت به دلیل مقاومت حرارتی بالا، استحکام مکانیکی خوب و عایق الکتریکی بودن در تولید قطعات صنعتی استفاده میشود. ویژگیهای حرارتی و مکانیکی باکالیت آن را برای استفاده در شرایط سخت کاری مناسب میسازد. فرآیند قالبگیری باکالیت به دلیل استفاده از رزین فنولیک، قطعاتی با دوام بالا تولید میکند. محدودیتهای طراحی قالبهای باکالیت در مقایسه با مزایای آن، قابل چشمپوشی است. مواد اولیه در قالبهای باکالیت نیز به گونهای انتخاب میشوند که این ویژگیها را تقویت کنند.
مهمترین عوامل تأثیرگذار بر کیفیت قالبگیری باکالیت چیست؟
مهمترین عوامل تأثیرگذار بر کیفیت قالبگیری باکالیت شامل دما، فشار، زمان پخت، و کیفیت مواد اولیه است. تأثیر فشار و دما بر کیفیت قالبگیری باکالیت بسیار زیاد است و باید به دقت کنترل شود. مواد اولیه در قالبهای باکالیت باید دارای کیفیت بالا و خواص مناسب باشند. ماشینهای قالبگیری باکالیت و تنظیمات آنها نیز نقش مهمی در کیفیت محصول نهایی دارند. تحلیل جریان مواد در قالبهای باکالیت به تعیین بهترین شرایط فرآیند کمک میکند.
چگونه میتوان عیوب قالبگیری باکالیت را کاهش داد؟
کاهش عیوب رایج در قالبگیری باکالیت و روشهای رفع آن، نیازمند کنترل دقیق فرآیند و استفاده از مواد اولیه با کیفیت است. تنظیم دقیق دما و فشار، بهینهسازی سیستمهای راهگاهی و خنککننده و استفاده از مواد اولیه مناسب از جمله این راهکارها هستند. تحلیل جریان مواد در قالبهای باکالیت به شناسایی و رفع این عیوب کمک میکند. استانداردهای طراحی قالبهای باکالیت نیز در کاهش این عیوب مؤثر است. روشهای بهینهسازی قالب برای تولید انبوه نیز باید به گونهای باشند که از بروز این عیوب جلوگیری کنند.
تفاوت بین قالبگیری باکالیت و پلاستیکهای دیگر چیست؟
تفاوت بین قالبگیری باکالیت و ترموپلاستیکها در این است که باکالیت یک ترموست است و پس از پخت، ساختاری سخت و غیرقابل انعطاف پیدا میکند، در حالی که ترموپلاستیکها را میتوان چندین بار ذوب و دوباره شکل داد. ویژگیهای حرارتی و مکانیکی باکالیت به عنوان یک ترموست، با ترموپلاستیکها متفاوت است. فرآیند قالبگیری باکالیت نیاز به دما و فشار بالاتری نسبت به ترموپلاستیکها دارد. محدودیتهای طراحی قالبهای باکالیت نیز با ترموپلاستیکها تفاوت دارد. مواد اولیه در قالبهای باکالیت نیز با ترموپلاستیکها متفاوت است.
بهترین روش خنککاری در قالبگیری باکالیت کدام است؟
روشهای خنککاری در قالبگیری باکالیت نقش مهمی در کیفیت محصول نهایی دارد. استفاده از سیستمهای خنککننده با کانالهای مناسب و توزیع یکنواخت دما در قالب، بهترین روش برای خنککاری باکالیت است. تحلیل جریان مواد در قالبهای باکالیت به تعیین بهترین مکان برای قرارگیری کانالهای خنککننده کمک میکند. استانداردهای طراحی قالبهای باکالیت نیز مشخصات سیستم خنککننده را تعیین میکنند. ماشینهای قالبگیری باکالیت و تنظیمات آنها باید به گونهای باشند که فرآیند خنککاری به طور دقیق کنترل شود.